By Walt Boyes
What is Remanufacturing? What are Differences & Processes?
There’s a great deal of confusion over what the difference between remanufacturing, refurbishing, reconditioning, and repairing for instrumentation and control valves. Let’s see if we can end the confusion.
Automation Service – Remanufactured vs. Refurbished
Remanufacturing does not mean refurbishing. When you refurbish, or recondition, or repair an instrument or control valve, you work on a single, already built product, and you try to bring it back to working condition by repairing the problem that caused the unit to fail. The instrument isn’t necessarily checked for any other failure points. So, when you get the instrument or valve back and install it, you can easily have an “infant mortality” failure on installation and start-up.
When you remanufacture, it means that you break the instrument or control valve into components, restore those components, and put them into stock. When you get an order for a specific valve or instrument, you pull from stock those remanufactured components and you build a complete device from them. It isn’t refurbished, it is remanufactured. Automation Service is proud to say “re-made in the USA.”
Remanufacturing Process
A major difference between refurbishing, or repairing an instrument and remanufacturing it is the process. Remanufacturing uses the same level of quality and reliability control that manufacturing does. It is built into the process. Refurbishing or repairing an instrument doesn’t use that same level of quality or reliability.
Here’s how it is done at Automation Service:
Automation Service’s recycling program, which is the most extensive in the automation industry, receives raw material and scrap and used process controls and parts from customers. Customers earn credits against future purchases by sending in their scrap and used parts.
When they come in, controls are disassembled down to the individual component level, and worn or unusable parts are discarded and replaced with new ones. Reusable parts are restored and subjected to a rigorous quality control and inspection process.
These parts are now “ready to use” and after a thorough inspection, they are packaged and put into inventory.
When Automation Service receives an order for a control valve or instrument, the process is nearly identical to the original manufacturing process.
Parts are pulled from inventory and the instrument or control is built to order to your specifications, following very stringent quality standards. After manufacture, the unit is calibrated and thoroughly examined and tested once more for optimal working performance. Quality control checks that all order specifications are met and the unit meets all quality standards. Once a quality control technician signs off on the quality check, your remanufactured control is shipped to you.
Click here to learn more about validation of remanufactured control valves.
Remanufacturing Examples
Watch these videos to see our remanufacturing process for a variety of products.
- Remanufactured Rosemount® 1151: a 30-Second Tour
- Remanufactured 3051 Transmitters: 30 Second Tour
- Remanufactured Fisher Control Valves: Take a Tour in Less than a Minute
Contact us to learn more about what a remanufactured Fisher® control valve or remanufactured Rosemount® instrument could do for you.
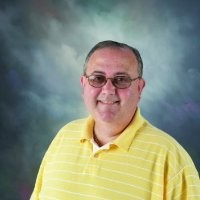
Walt Boyes has more than 40 years of experience in the automation industry, including Executive Committee experience in three companies, and board of directors service in both for-profit and not-for-profit companies. Walt is principal in Spitzer and Boyes LLC, a technology consulting firm assisting companies to better market their products in manufacturing and automation. He has contributed to many industry publications as both writer and editor. View Walt’s full bio.